Hydraulic tipper trailers, essential in industries like construction, agriculture, and waste management, demand high durability, precision, and reliability in their components. Manufacturing these trailers involves intricate processes, with CNC machining, forging, sheet metal fabrication, and welding playing pivotal roles.
The use of CNC machining, forging, and sheet metal fabrication is central to ensuring the structural integrity, durability, and functionality of these trailers.
This article delves into how and where these manufacturing processes are applied in hydraulic tipper trailer production.
CNC Machining
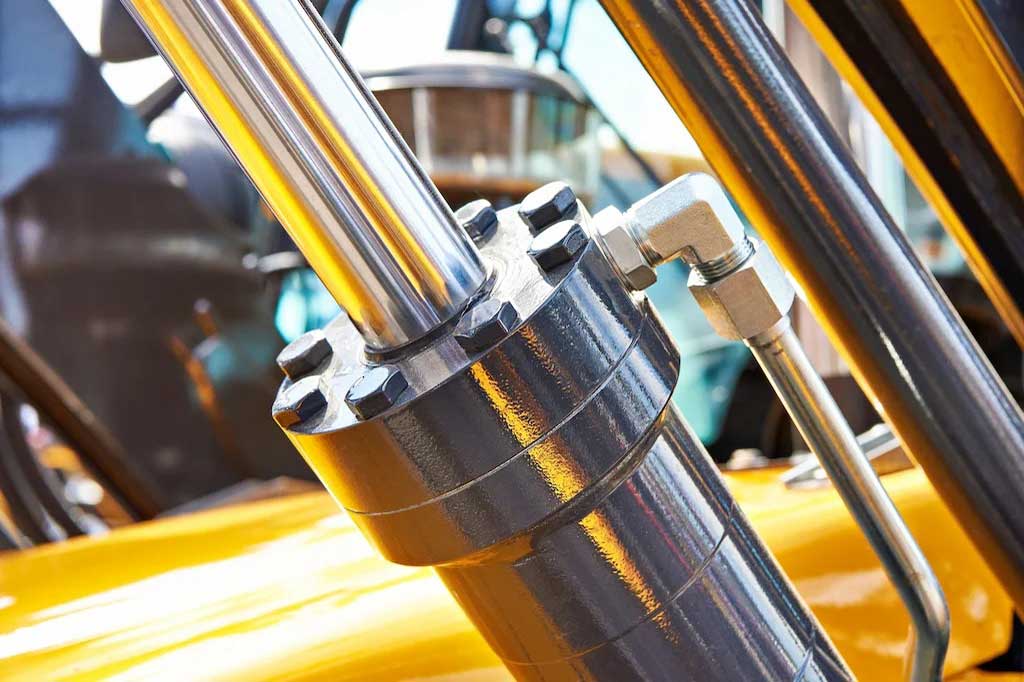
1. Precision Components Production
CNC (Computer Numerical Control) machining is a process that employs computerized controls and precision tools to shape parts from raw materials.
In hydraulic tipper trailer manufacturing, CNC machining is crucial for producing precision components that are integral to the trailer’s hydraulic system and structural integrity.
- Hydraulic System Components: CNC machining is used to create precision parts for hydraulic cylinders, pumps, and valves. The hydraulic system is the heart of the tipper trailer, responsible for lifting and lowering the trailer bed. Components such as piston rods, cylinder caps, and valve bodies require tight tolerances to ensure proper functioning and prevent leaks.
- Axles and Wheel Hubs: CNC machining is also used to manufacture axles and wheel hubs, ensuring they are perfectly aligned and balanced. These components must withstand the trailer’s load and the forces generated during tipping operations. High precision in their production is essential for safety and longevity.
2. Customization and Prototyping
Custom CNC machining allows for the rapid prototyping of hydraulic tipper trailer components. Manufacturers can create tailored parts to meet specific customer requirements, such as unique trailer sizes or load capacities. CNC machines can quickly switch from one design to another, facilitating efficient prototyping.
3. Structural Components and Frame Assembly
In addition to hydraulic system parts, CNC machining is used to produce structural components like mounting brackets, hinges, and locking mechanisms. These parts are essential for the trailer’s frame assembly, ensuring that all components fit together precisely. CNC machining ensures consistent quality and repeatability, crucial for mass production where uniformity is key.
Forging
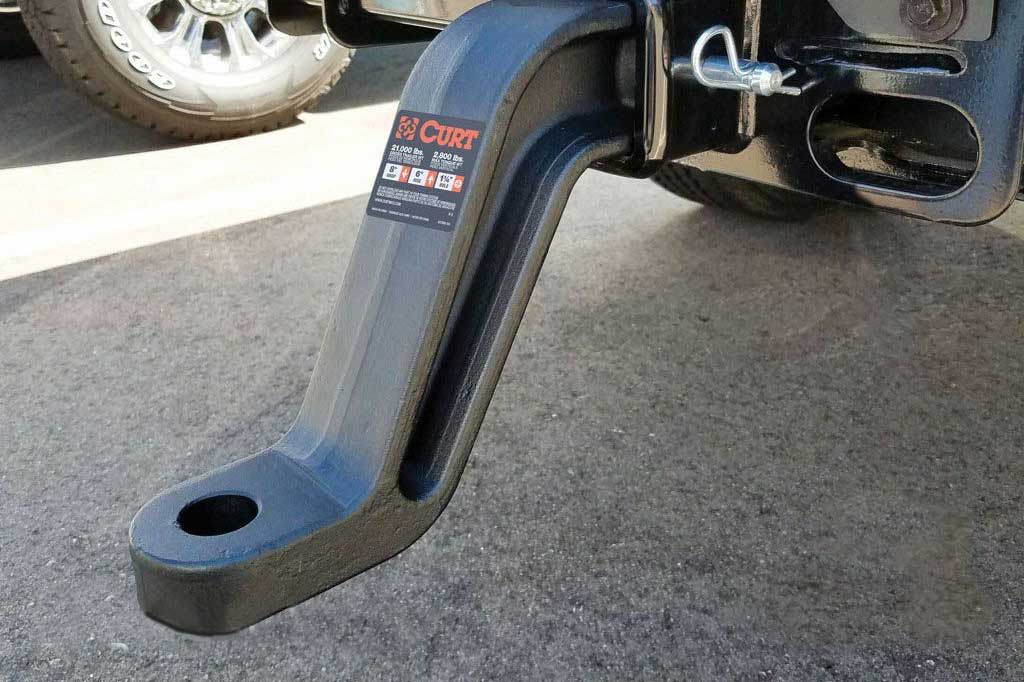
1. High-Strength Components
Forging is a manufacturing process where metal is shaped under high pressure, usually in a hot or cold state, to create strong and durable parts. These forged parts are less likely to fail under stress, making them ideal for use in critical areas of the trailer.
In hydraulic tipper trailer manufacturing, metal forging is used to produce components that need to withstand heavy loads and harsh conditions, such as:
- Trailer Hitch and Couplings: The trailer hitch and couplings are critical components that connect the tipper trailer to the towing vehicle. These parts must endure significant stress and pressure, especially during tipping operations. Forging is ideal for producing these components due to the increased strength and toughness it imparts to the metal.
- Hydraulic Cylinder Components: Forged components such as cylinder rods and end caps are often used in the hydraulic cylinder. The forging process ensures that these parts are robust and resistant to fatigue, reducing the risk of failure under heavy loads.
2. Cost-Effective Mass Production
While forging is a more capital-intensive process compared to others, it becomes cost-effective in mass-production scenarios.
Hydraulic tipper trailers, especially those produced in large quantities, benefit from forging because it allows manufacturers to produce large numbers of identical, high-strength components efficiently. The consistency and quality of forged parts ensure that every trailer meets the required safety and performance standards.
3. Integration with CNC Machining
A forged axle may need to be machined to create precise mounting points or to achieve a smooth surface finish.
This integration of forging and CNC machining combines the strength benefits of forging with the precision of CNC machining, resulting in high-quality components that are both durable and accurate.
Sheet Metal Fabrication
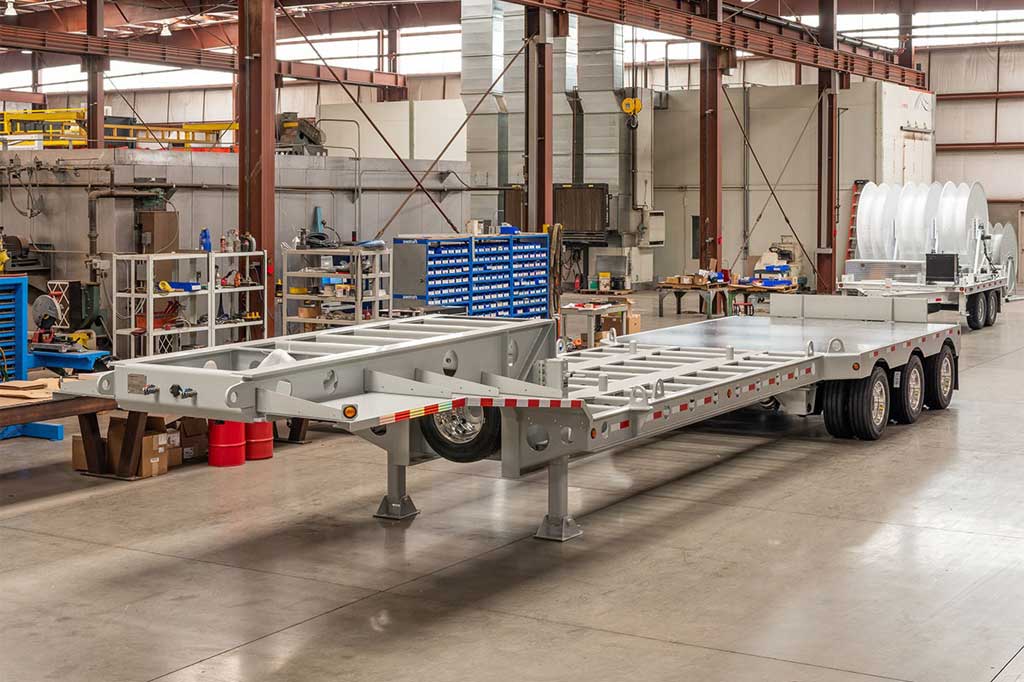
1. Trailer Body and Chassis Construction
In hydraulic tipper trailer manufacturing, sheet metal fabrication is crucial for constructing the trailer body, chassis, side panels, and enclosures.
- Trailer Bed: The trailer bed, or the tipping platform, is made from steel or aluminum sheets. Sheet metal fabrication allows manufacturers to cut and shape these sheets into the desired dimensions, ensuring a strong and durable platform capable of withstanding heavy loads. The bending process is particularly important for creating the sides and floor of the trailer bed, which must be both sturdy and resistant to deformation.
- Chassis Frame: The chassis frame, which supports the trailer bed and connects it to the axles, is another critical component made through sheet metal fabrication. The frame must be robust enough to handle the stresses of tipping operations while maintaining the trailer’s overall stability. Fabrication techniques like welding and riveting are used to assemble the frame components, ensuring a solid and secure structure.
2. Customization and Versatility
Sheet metal fabrication offers great versatility in design, allowing manufacturers to customize hydraulic tipper trailers according to specific requirements.
Whether it’s adjusting the size of the trailer bed, adding side extensions, or incorporating specialized features like toolboxes or tarp systems, sheet metal fabrication can accommodate a wide range of customizations.
3. Lightweight Construction with Aluminum
For applications where weight reduction is crucial, such as in agriculture or transportation, aluminum sheet metal is often used. Aluminum is lighter than steel but still offers sufficient strength for many trailer components. Sheet metal fabrication techniques are used to create lightweight yet durable parts, contributing to better fuel efficiency and easier maneuverability of the tipper trailer.
4. Surface Treatment and Finishing
After the sheet metal components are fabricated, they undergo surface treatment and finishing processes to enhance their durability and resistance to corrosion. Techniques such as powder coating, galvanizing, or painting are commonly applied to protect the metal surfaces from rust and wear, extending the lifespan of the hydraulic tipper trailer.
Welding
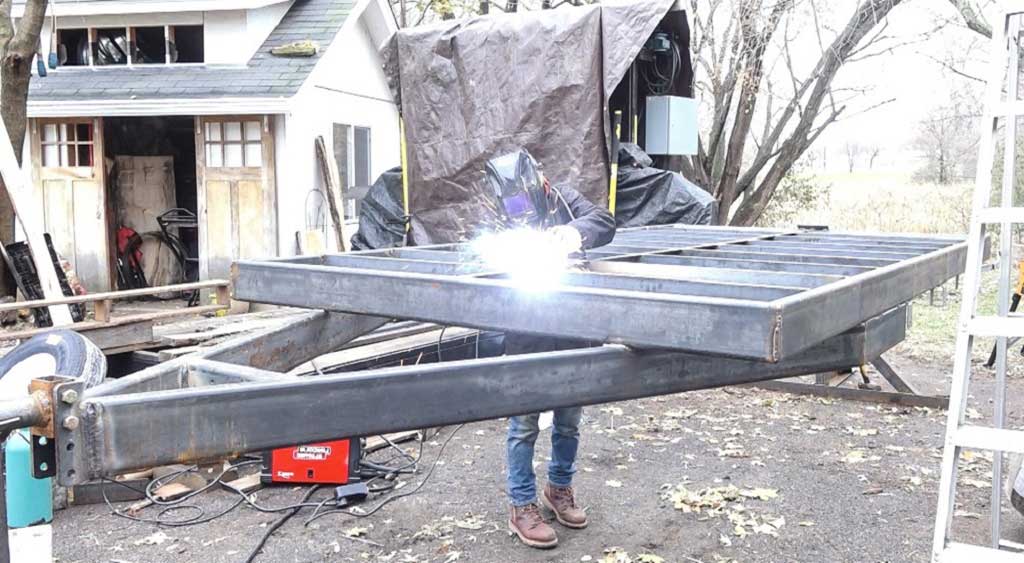
1. Structural Integrity and Assembly
Welding is a critical process in hydraulic tipper trailer manufacturing, used to join metal parts to create strong, permanent bonds. The structural integrity of the trailer depends on high-quality metal welding service, which ensures that components like the chassis, trailer bed, and hydraulic mounts are securely assembled.
- Chassis and Frame Welding: The chassis and frame form the backbone of the tipper trailer. Welding these components together requires precision and strength, as any weak welds could compromise the trailer’s ability to withstand heavy loads and rough terrain.
- Hydraulic System Mounts: The hydraulic system, including the cylinders and pumps, must be securely mounted to the trailer’s frame. Welding is used to attach these mounts, ensuring they can endure the stresses of lifting and tipping heavy loads without shifting or failing.
2. Versatility and Adaptability
Welding is highly adaptable, making it suitable for joining various materials used in hydraulic tipper trailers, such as steel and aluminum. This versatility allows manufacturers to create trailers with different material combinations, optimizing for weight, strength, and cost based on the specific application.
3. Enhancing Load-Bearing Capacity
Welding contributes to the trailer’s overall load-bearing capacity by reinforcing joints and connections. Proper welding techniques ensure that the trailer can handle maximum loads without risk of structural failure, providing safety and reliability during operation.
4. Repair and Maintenance
In addition to assembly, welding is crucial for the repair and maintenance of hydraulic tipper trailers. Trailers often face wear and tear, especially in demanding environments. Welding allows for the reinforcement or replacement of damaged components, extending the life of the trailer. Field repairs are also possible with portable welding equipment, ensuring minimal downtime for the trailer.
Conclusion
The manufacturing of hydraulic tipper trailers is a complex process that requires the integration of various advanced manufacturing techniques.
CNC machining ensures precision and customization, forging provides strength and durability, sheet metal fabrication offers versatility and structural integrity, and welding guarantees strong, permanent bonds that enhance the trailer’s overall performance.
Together, these processes enable manufacturers to produce hydraulic tipper trailers that meet the rigorous demands of their applications, ensuring efficiency, safety, and longevity.